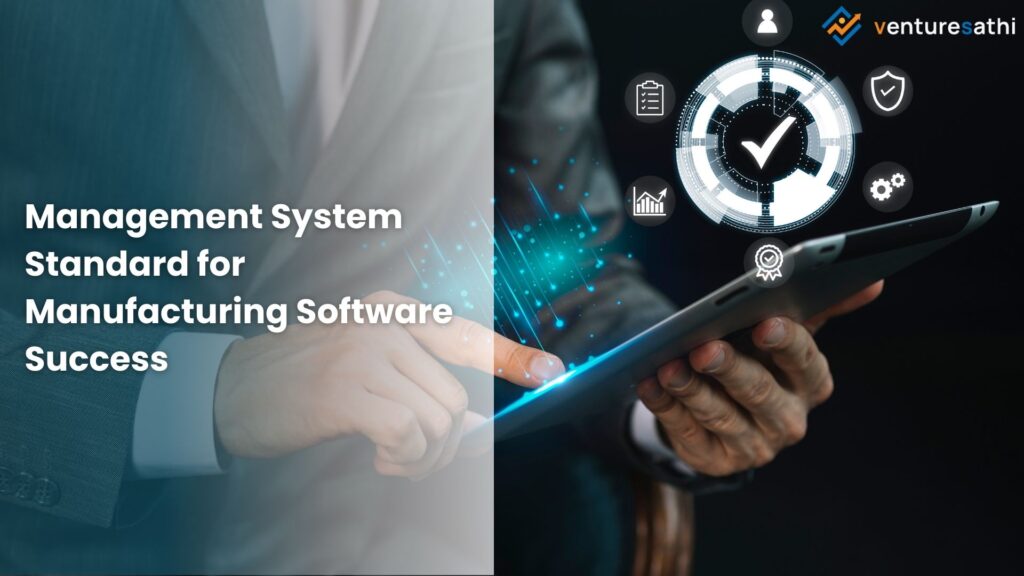
Are you looking to enhance the efficiency and quality of your manufacturing software? Wondering how to ensure the safety of your employees and the security of your data? Look no further than the Management System Standards designed to elevate your operations to the next level.
Imagine a system that guarantees the quality of your products and prioritizes your workforce’s health and safety. Picture a framework that protects your sensitive information and ensures minimal environmental impact. These are the promises of the Management System Standards, including the Quality Management System (QMS) ISO-9000-2015, the Environmental Management System (EMS), the Occupational Health and Safety Assessment Series (OHSAS), and the Information Security Management System (ISMS).
By adhering to these standards, manufacturing software can optimize its processes, improve product quality, and mitigate risks. These standards are not just guidelines; they are a commitment to excellence in manufacturing, ensuring that your software meets the highest standards of quality, safety, and security.
In this blog, we’ll delve into each of these Management System Standards, exploring their benefits, implementation strategies, and how they can transform your manufacturing software. Let’s unlock the potential of your software and take it to new heights of success!
Looking to enhance your manufacturing software’s performance and compliance? Venturesathi offers tailored solutions to implement Management System Standards effectively. Get in touch today!
Quality Management System (QMS) ISO-9000-2015
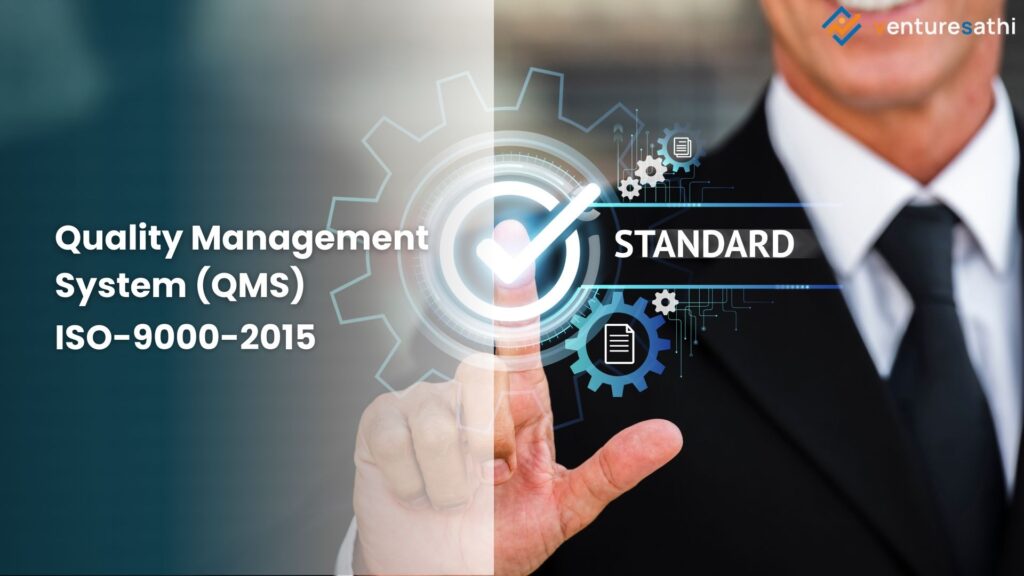
The ISO 9000 series of standards, particularly ISO 9001:2015, plays a crucial role in shaping the quality management systems (QMS) of organizations worldwide. It establishes a framework for organizations to ensure that their products and services consistently meet customer requirements and comply with regulatory standards. ISO 9000-2015 emphasizes the importance of understanding customer needs, aligning organizational objectives with customer expectations, and continuously improving processes to enhance customer satisfaction.
One of the key aspects of ISO 9000-2015 is its focus on process management. It encourages organizations to manage their activities as processes, measure the capability of these processes, and identify opportunities for improvement. By adopting a process approach, organizations can streamline their operations, reduce waste, and improve overall efficiency.
ISO 9000-2015 also promotes a culture of continuous improvement. It encourages organizations to regularly evaluate their performance, set challenging goals, and empower employees to make improvements. This continuous improvement mindset helps organizations stay competitive in a dynamic business environment and adapt to changing customer needs and market conditions.
Overall, QMS ISO 9000-2015 is a foundational standard for organizations looking to enhance their quality management practices and achieve sustained success in the custom manufacturing industry. Its principles and guidelines are essential for organizations to build a robust quality management system that drives customer satisfaction and business excellence.
Environmental Management System (EMS) ISO 14001
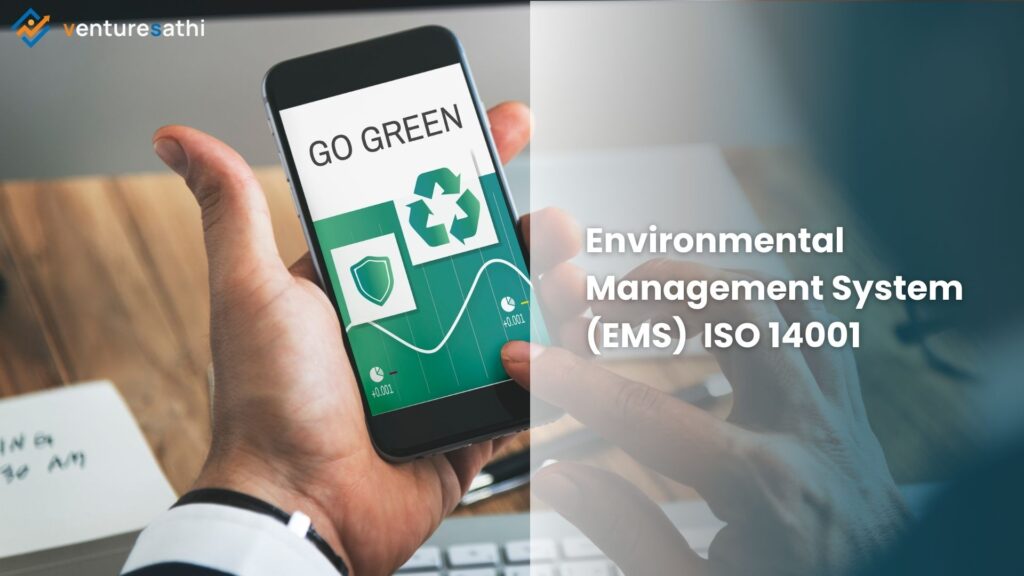
The Environmental Management System (EMS) is a crucial framework for organizations, including those in custom manufacturing software, seeking to manage and improve their environmental performance effectively. EMS, often aligned with ISO 14001 standards, provides a structured approach to identifying, controlling, and mitigating environmental impacts associated with business operations.
In custom manufacturing software development, where innovation and efficiency are paramount, implementing an EMS ensures a holistic approach to addressing environmental concerns. This includes assessing resource consumption, waste generation, energy usage, and emissions associated with software development processes.
By adopting ISO 14001 standards, organizations can establish clear environmental objectives and targets tailored to their specific operations. This involves conducting thorough environmental assessments, identifying legal requirements, and implementing measures to ensure compliance while striving for continuous improvement.
Maintaining an EMS within custom manufacturing software not only helps mitigate environmental risks but also offers several business benefits. It enhances corporate reputation and stakeholder confidence by demonstrating a commitment to environmental stewardship. Moreover, it can lead to cost savings through resource efficiency and waste reduction initiatives.
Employee morale and engagement are also positively influenced by an EMS, as it fosters a culture of environmental responsibility and sustainability within the organization. By aligning with emerging trends such as circularity and environmental stewardship, companies can stay ahead of regulatory requirements and market expectations.
Integrating an EMS into custom manufacturing software practices is essential for achieving environmental sustainability while driving business success. By prioritizing environmental considerations and adhering to recognized standards, organizations can mitigate risks, enhance their reputation, and contribute to a more sustainable future.
Occupational Health and Safety Assessment Series (OHSAS)
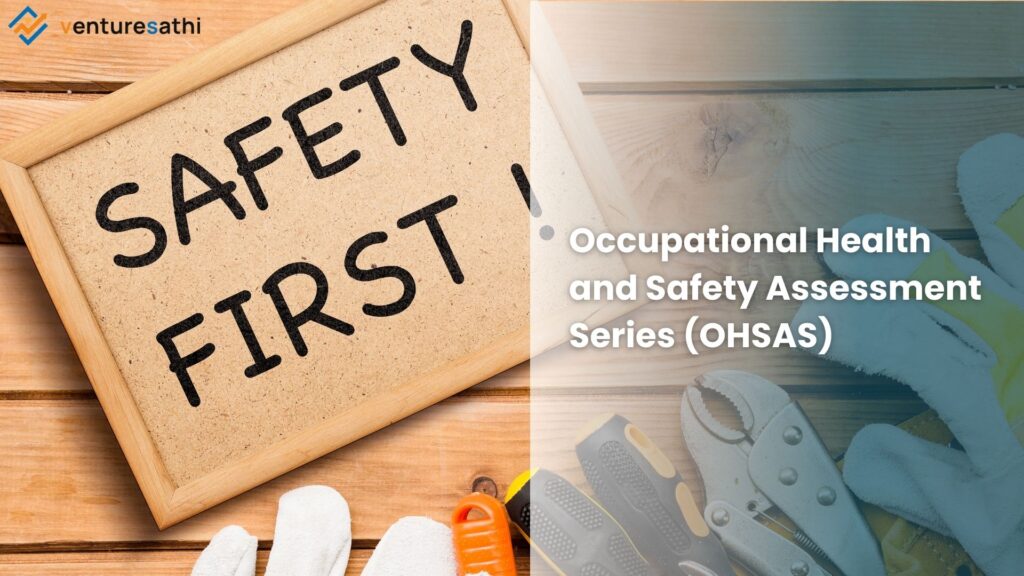
OHSAS 18001, the Occupational Health, and Safety Assessment Series, served as a fundamental standard for occupational health and safety management systems (OHSMS) worldwide. It provided a structured framework for organizations to effectively control and improve their health and safety performance, fostering a safe working environment for employees. This standard, developed in 1999, aimed to streamline and unify various national standards and certification schemes, thus eliminating confusion and fragmentation in the market.
The adoption of OHSAS 18001 by organizations allowed them to demonstrate their commitment to occupational health and safety by implementing robust management systems. It included requirements for developing OHS policies and procedures, conducting risk assessments, establishing training programs, and fostering communication on health and safety matters. By adhering to OHSAS 18001, businesses could reduce accidents, improve morale, and mitigate workers’ compensation costs.
However, with the publication of ISO 45001 in 2018, OHSAS 18001 was eventually replaced. ISO 45001, the international standard for occupational health and safety management systems, offers a more comprehensive and updated approach to managing workplace health and safety. Organizations previously certified to OHSAS 18001 were encouraged to migrate to ISO 45001 to retain recognized certification.
Despite its obsolescence, understanding OHSAS 18001 remains crucial, especially in industries like custom manufacturing software. Prioritizing occupational health and safety not only protects employees but also enhances organizational reputation, reduces costs, and fosters a culture of safety. OHSAS 18001 was phased out in September 2021 and is no longer issued or valid. ISO 45001 has replaced it, offering a more updated and comprehensive framework for occupational health and safety management.
Information Security Management System (ISMS) ISO/IEC 27001
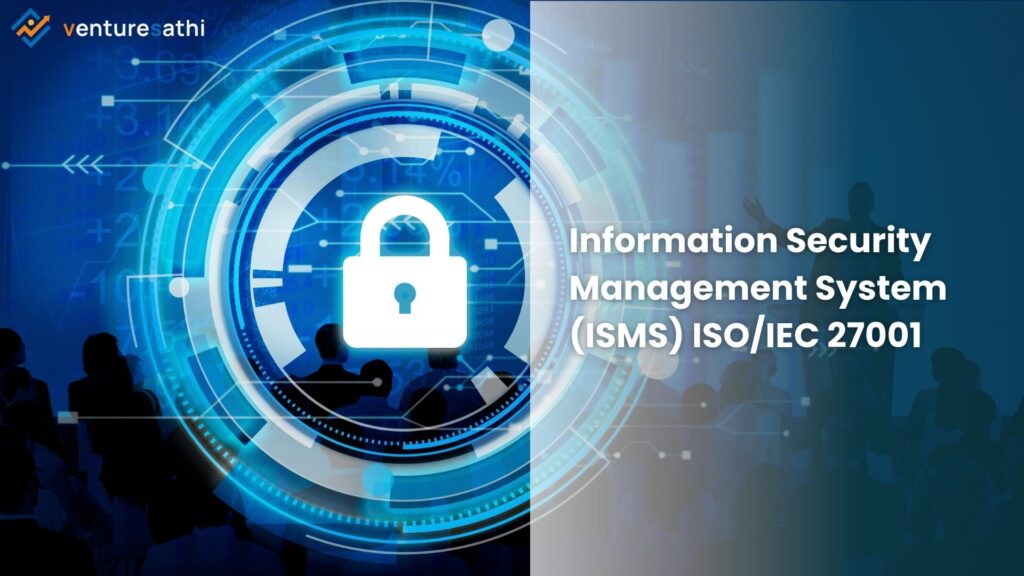
An Information Security Management System (ISMS) is an essential framework for systematically managing sensitive data within custom manufacturing software for organizations. It encompasses policies, procedures, and practices designed to safeguard valuable information assets against unauthorized access, use, disclosure, or destruction. ISMS works by providing a structured approach to managing and protecting information assets and addressing employee behavior, processes, and technology.
ISO/IEC 27001 serves as the international standard for ISMS, outlining requirements and best practices for establishing, implementing, maintaining, and continually improving information security management. By adhering to ISO/IEC 27001, organizations can effectively manage risks related to data security, ensure compliance with applicable laws and regulations, and enhance their competitive edge.
The benefits of an ISMS within custom manufacturing software are substantial. Firstly, it protects sensitive data, including customer information, intellectual property, and financial data, from breaches and unauthorized access. Secondly, it helps organizations meet regulatory compliance requirements, reducing the risk of hefty fines associated with violations. Thirdly, it ensures business continuity by minimizing disruptions caused by security incidents, thereby safeguarding operations and reputation. Additionally, ISMS reduces costs by prioritizing security measures and preventing indiscriminate spending on unnecessary defenses. Moreover, it fosters a culture of security awareness among employees, enhancing overall organizational resilience against emerging threats.
Implementing an ISMS involves a comprehensive risk assessment to identify potential threats and vulnerabilities, followed by the establishment of appropriate controls and mitigation measures. ISO/IEC 27001 guides this process, ensuring that organizations can effectively protect their information assets while adapting to evolving security challenges. Overall, ISMS is indispensable in custom manufacturing software, offering a robust framework for safeguarding sensitive data and ensuring the security and integrity of operations.
How to Implement These Standards?
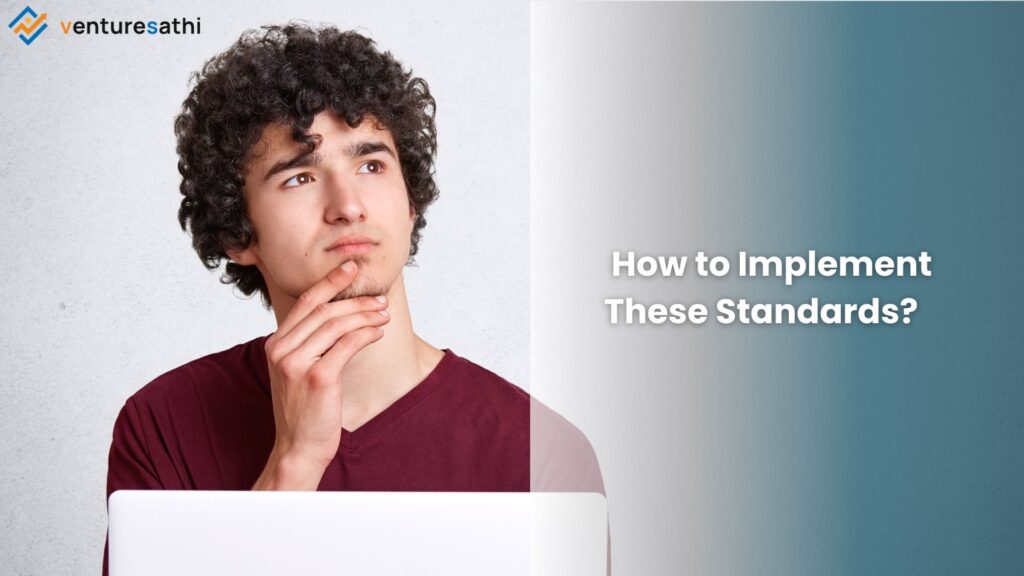
To implement these standards in manufacturing software development, consider the following solutions:
- Software Tools: Use software tools that help manage quality, environmental, health and safety, and information security aspects. These tools can assist in documenting processes, tracking compliance, and managing risks.
- Training Programs: Implement training programs for employees to ensure they understand the standards and their compliance roles. This can include online courses, workshops, and seminars.
- Consulting Services: Consider hiring consultants with expertise in implementing these standards. They can provide guidance, conduct audits, and help develop strategies for compliance.
- Internal Audits: Conduct regular internal audits to assess compliance with the standards and identify areas for improvement. This can help ensure that the implemented systems are effective and efficient.
- Integration of Systems: Integrate the different management systems to streamline processes and reduce duplication of efforts. This can improve overall efficiency and effectiveness.
- Performance Metrics: Establish performance metrics to measure the effectiveness of the implemented systems. This can help track progress and identify areas for further improvement.
- Continuous Improvement: Foster a culture of continuous improvement by encouraging feedback from employees and stakeholders. This can help identify new opportunities for improvement and ensure that the organization remains competitive.
Takeaway
Implementing Management System Standards such as QMS, EMS, OHSAS, and ISMS is crucial for enhancing the performance, quality, safety, and security of your manufacturing software. These standards improve your operations and demonstrate your commitment to excellence and compliance with international best practices.
To unlock the full potential of your manufacturing software and ensure its success in the market, consider integrating these standards into your development and management processes. Embracing these standards will not only benefit your software but also your business, enhancing your reputation, reducing risks, and increasing customer satisfaction.
If you’re ready to take your manufacturing software to the next level, contact us today. Our expert team specializes in developing software that meets and exceeds industry standards, helping you achieve your business goals efficiently and effectively. Let’s collaborate to create innovative solutions that drive your success.